Chinese E cargo tricycles change game
Sales Network 2022-06-14
In the global landscape of logistics and short-distance transportation, Chinese electric cargo tricycles have emerged as a game-changer, combining affordability, efficiency, and eco-friendliness. As a website editor specializing in exporting these vehicles, I invite you to explore how China’s manufacturing prowess and innovative R&D capabilities are reshaping cargo transportation Overview: Precision Engineering Meets Practical Needs
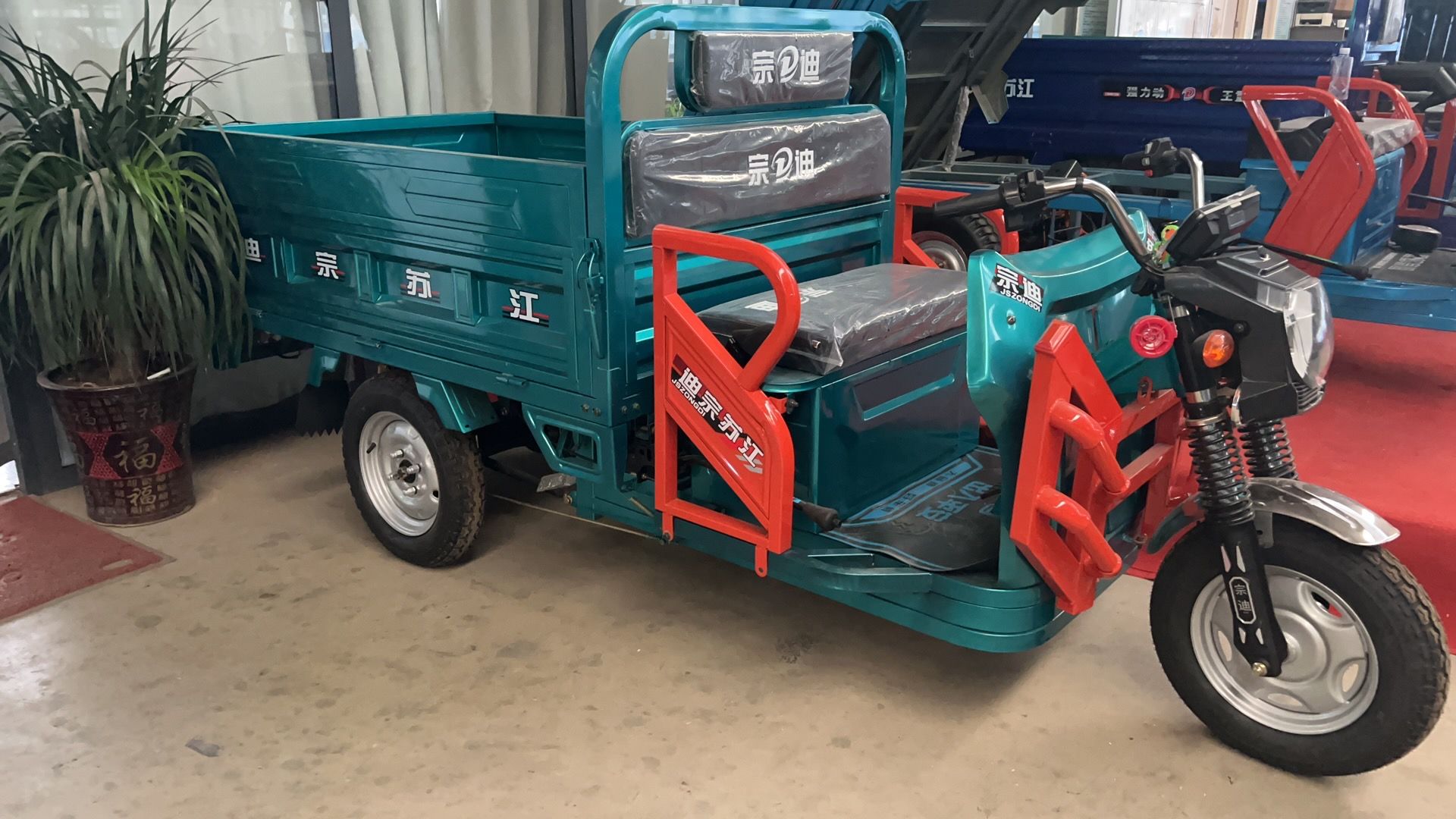
China’s electric tricycle cargo industry has evolved through decades of refinement. Vehicles are categorized into Three-Open Type (separate cab and cargo areas), Four-Open Type (enhanced accessibility), and Semi-Canopy Type (partial weather protection), each designed for specific scenarios. Equipped with 500W+ brushless motors and 60V/72V batteries, these tricycles achieve a 300-800kg payload capacity with a 60-100km range per charge – perfect for urban deliveries, agricultural markets, or industrial park logistics. A fruit distributor in Southeast Asia, for instance, reduced last-mile costs by 40% after replacing diesel trucks with a 10-unit tricycle fleet.
2. Manufacturing Advantages: Where Scale Meets Sophistication
China’s supply chain ecosystem – from lithium battery production to stamping workshops – enables unparalleled cost efficiency. A typical 1.5m³ cargo bed model costs USD 800-1,200 FOB, 30-50% lower than European equivalents, without compromising quality. Major manufacturers like Loncin and Wuyang have obtained ISO 9001 and CE certifications, while emerging brands such as Dayun leverage automotive-grade welding robots for chassis construction. Annual industry output exceeds 2 million units, supported by 120+ specialized component suppliers.
3. Market Dynamics: Customization as Standard
Domestic sales growth (CAGR 8.7% 2020-2023) fuels export innovation. Key trends include:
- Modular Design: Kenyan clients mix cab styles with removable cargo modules
- Battery Flexibility: Nigerian buyers opt for dual-charging ( Upgrades**: Brazilian logistics firms install IoT trackers for fleet management
Production cycles average 15-30 days for standard models, extendable to 45 days for customized orders. Sea freight to major ports takes 25-35 days, with manufacturers increasingly offering CKD kits to reduce tariffs.
4. Competitive Edges: Beyond Price Leadership
While cost efficiency attracts initial attention, clients stay for:
- Terrain-Specific Tuning: Himalayan-grade gearboxes for Nepalese mountain roads
- After-Sales Networks: 18-month warranty with local spare parts hubs in 30+ countries
- Regulatory Compliance: Pre-installed reflectors, speed limiters per EU Regulation 168/2013
A case in point: A Mexican e-commerce platform achieved 98% vehicle uptime through predictive maintenance agreements with their Jiangsu-based supplier.
5. Future-Proofing Partnerships
The industry is pivoting towards:
Green Manufacturing: 85% steel recycling rates in Shandong production clusters
Battery Swapping Ecosystems: 3-minute battery changes via partnership stations
AI-Driven Energy Management: 15% range extension through adaptive power algorithms